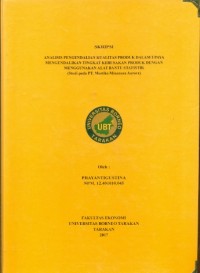
Analisis Pengendalian Kualitas Produk Dalam Upaya Mengendalikan Tingkat Kerusakan Produk Dengan Menggunakan Alat Bantu Statistik (Studi Pada PT. Mustika Minanusa Aurora)
Pengarang : Prayantigustina - Personal Name;
Perpustakaan UBT : Universitas Borneo Tarakan., 2017XML Detail Export Citation
Abstract
PT Mustika Minanusa Aurora sebagai merupakan salah satu perusahaan penampung udang (cool storage), Sebagai perusahaan yang bergerak dalam industri perikanan dan perairan dan yang dihasilkan adalah udang beku. Untuk menjaga kualitas dan demi menjaga kepercayaan konsumen untuk menghasilkan produk yang berkualitas, sejak lama perusahaan telah memperoleh sertifikat ASAP sebagai pengakuan bahwa perusahaan telah menerapkan manajemen mutu yang baik dan sesuai dengan pedoman standar mutu yang berlaku. Dan dalam kegiatan produksinya, perusahaan selalu berusaha untuk menghasilkan produk yang baik dan menekan kerusakan produk atau misdruk yang tinggi dengan menetapkan standar toleransi misdruk sebesar 5 % dari jumlah produksi. Penelitian ini bertujuan untuk mengetahui bagaimana pelaksanaan sistem pengendalian kualitas dengan alat bantu statistic dapat membantu dan mendapatkan manfaat dari hasil tersebut. Analisis pengendalian kualitas dilakukan menggunakan alat bantu statistik berupa check sheet, histogram, peta kendali p, diagram pareto dan diagram sebab-akibat. Check sheet dan histogram digunakan untuk menyajikan data agar memudahkan dalam memahami data untuk keperluan analisis selanjutnya. Peta kendali p digunakan untuk memonitor produk yang rusak apakah masih berada dalam kendali statistik atau tidak. Kemudian dilakukan identifikasi terhadap jenis cacat yang dominan dan menentukan prioritas perbaikan menggunakan diagram pareto. Langkah selanjutnya adalah mencari faktor-faktor yang menjadi penyebab terjadinya kerusakan produk menggunakan diagram sebab akibat untuk kemudian dapat disusun sebuah rekomendasi atau usulan perbaikan kualitas. Hasil analisis peta kendali p menunjukkan bahwa proses berada dalam keadaan tidak terkendali atau masih mengalami penyimpangan. Hal ini dapat dilihat pada grafik kendali dimana titik berfluktuasi sangat tinggi dan tidak beraturan, serta banyak yang keluar dari batas kendali. Berdasarkan diagram pareto, prioritas perbaikan yang perlu dilakukan adalah untuk jenis kerusakan yang dominan yaitu kerusakan cacat (40,90%), ekor gripis (25,50%), kulit lembek (20,45 %) dan kulit merenggang (13,65 %). Dari analisis diagram sebab akibat dapat diketahui faktor penyebab misdruk berasal dari faktor manusia/ pekerja, mesin produksi, metode kerja, material/ bahan baku dan lingkungan kerja.
PT Mustika Minanusa Aurora as one of the shrimp storage company (cool storage), As a company engaged in the fishery and aquatic industry and produced is frozen shrimp. To maintain the quality and in order to maintain the trust of consumers to produce quality products, the company has since secured ASAP certification in recognition that the company has implemented a good quality management and in accordance with applicable quality standard guidelines. And in its production activities, the company always strives to produce good products and suppress high product or misrukuk damage by setting the standard of misdruk tolerance of 5% of total production. Nevertheless, after the results of the research indicate the fact that the level of misdruk is still in the repair period and even there are still misdruk that exceed the standard of tolerance set. This study aims to find out how the implementation of quality control systems with statistical tools can help and benefit from these results. Quality control analysis is performed using statistical tools such as check sheet, histogram, p control chart, pareto diagram and cause-effect diagram. Check sheets and histograms are used to present the data to make it easier to understand the data for later analysis. The control chart p is used to monitor the damaged product whether it is still under statistical control or not. It then identifies the dominant type of defect and determines the priority of improvement using the pareto diagram. The next step is to look for factors that cause the occurrence of product damage using cause and effect diagram to then be prepared a recommendation or suggestion of quality improvement. The result of p control map analysis indicates that the process is in an uncontrolled condition or is still deviated. This can be seen in the control charts where the points fluctuate very high and irregular, and many are out of control limits. Based on the pareto diagram, the priority of improvement that needs to be done is for the dominant type of damage that is defect damage (40,90%), gripis tail (25,50%), soft skin (20,45%) and stretch skin (13,65% ). From the analysis of cause and effect diagram can be known factors causing misdruk come from human factor / worker, production machine, working method, material / raw material and work environment.